While unboxing a new shampoo tailored specifically for Indian hair types, I couldn't help but marvel at the thought and precision of its creation, from the ingredients to the packaging and even the marketing. It made me realize that bringing such a product to market isn’t easy. It requires careful planning, coordination, and an efficient process.
So, how do companies, especially those handling complex products, manage the intricacies of development and production? The answer lies in the best product lifecycle management (PLM) software.
I discovered how these systems help businesses streamline product development from ideation to launch by evaluating the top PLM tools. They centralize documents, track progress, and enable seamless team collaboration, ensuring every stage is meticulously managed and optimized.
Keep reading if you want to kickstart a product-led business or improve processes in your existing product development strategy. PLM tools can help you bring your ideas to life more efficiently and effectively.
6 best PLM software: My picks for 2025
-
Siemens Teamcenter for seamless integration of product data and workflows across engineering and manufacturing (pricing available on request)
-
Arena PLM & QMS for combining product lifecycle management with quality management to ensure compliance (pricing available on request)
-
OpenBOM for simplifying BOM management and seamless CAD tool integration in the cloud (free 14-day trial available, prices starting at $100/seat/mo)
-
Onshape for real-time cloud-based collaboration with 3D CAD and PLM features (free plan available, prices for premium version starting at $1500/seat/annum)
-
Propel for a customer-centric PLM platform integrated with Salesforce (pricing available on request)
-
Duro for a simple, fast cloud-based PLM solution tailored for startups and small businesses (pricing available on request)
* These PLM tools are top-rated in their category, according to G2 Grid Reports.
My top 6 PLM software recommendations for 2025
The best PLM software is designed to help businesses streamline product development, enhance cross-team collaboration, and accelerate time to market. As I evaluated these tools, I saw firsthand how they centralize product data, improve design workflows, and ensure greater transparency throughout the entire product journey.
How did I find and evaluate the best PLM software?
By analyzing G2 reviews and G2’s Grid Reports, I comprehensively understood each PLM tool’s features, ease of use, and overall value. I relied on verified reviews from professionals with hands-on experience to validate my findings.
I also used AI to analyze patterns in user feedback, ensuring I captured a wide range of perspectives on the software’s effectiveness in streamlining product development, improving collaboration, and enhancing product lifecycle management. The screenshots featured in this article may be a mix of those from G2 reviews and vendor-provided visuals.
By combining G2 insights with expert feedback, I’ve compiled a list of the best PLM software solutions to help you choose the right tool for your organization’s needs.
What makes PLM software worth it: My opinion
When evaluating the best PLM software, I focus on several key features to determine its effectiveness for product development teams and manufacturers:
- Product data management and collaboration: A strong PLM system should be a centralized hub for product information, design files, specifications, Bill of Materials, and change orders. I evaluate how easily teams can upload, organize, and update product data throughout the lifecycle. I also assess searchability, version control, and whether team members can collaborate in real time, providing comments, annotations, and approvals across departments like engineering, manufacturing, and quality assurance.
- Change management and process automation: PLM software should streamline engineering change orders (ECOs) and product updates without introducing chaos. I look at how easily users can initiate, review, approve, and implement changes. The best platforms offer visual change histories, automated approval routing, and integration with computer aided design (CAD) and ERP systems to ensure that changes flow smoothly across the organization without missing critical updates.
- BOM management: Managing complex BOMs across different product variants is a core function of PLM. I evaluate whether the software allows dynamic BOM creation, versioning, and easy comparison between versions. The ideal system should also support multi-level BOMs and integrations with manufacturing resource planning (MRP) systems to ensure production-ready accuracy.
- Integration with design and manufacturing tools: A PLM solution must integrate smoothly with CAD, computer-aided-manufacturing (CAM), ERP, and other essential systems. I evaluate how easily data flows between platforms without duplication or manual entry. Good integrations minimize data silos, improve traceability, and ensure that designs and production plans are always synchronized across departments.
- Scalability and customization: PLM software should scale with businesses as they grow and products become more complex. I assess whether the tool offers customization options like configurable workflows, dashboards, and reporting tools. A great PLM system should allow organizations to tailor the platform to their specific product types, compliance requirements, and operational processes without constant reliance on external consultants.
- Compliance and quality management: Regulatory compliance is a big challenge for the automotive, aerospace, and medical device industries. I assess whether the PLM platform includes built-in support for quality processes (like CAPA, ISO standards, FDA regulations) and audit trails. I also look for documentation control, operational risk management tools, and electronic signature support to help teams maintain compliance with minimal friction.
- Allow users to create and manage product configurations and bill of materials (BOM)
- Deliver features for requirements tracking and engineering change management
- Provide a centralized repository to manage product data throughout its lifecycle
- Maintain product documentation, CAD models, drawings, and technical specifications
- Manage product costs by tracking the costs of the components defined in BOMs and recipes
- Comply with quality standards and regulations or with customer-specific requirements
- Include simulation features to manage product testing scenarios in virtual environments
- Facilitate collaboration with suppliers, subcontractors, and other stakeholders
- Assist manufacturers with process planning across multiple locations
- Analyze product development KPIs and monitor engineering performance
This data was pulled from G2 in 2025. Some reviews have been edited for clarity.
1. Siemens Teamcenter
Siemens Teamcenter stands out as a comprehensive product lifecycle management (PLM) solution, especially suited for organizations handling complex product development. Reviewers often describe it as a reliable tool for centralizing and managing product-related data, though it does have a few usability challenges.
One feature I see getting much praise is Teamcenter’s ability to manage, store, and retrieve product data. G2 reviewers frequently highlight how it eliminates the need for scattered spreadsheets and disconnected storage systems. Once implemented, users say it becomes a single source of truth that enhances data visibility and streamlines design and documentation workflows across teams.
There’s much love for how this tool handles real-time collaboration across departments. Many users appreciate how it enables engineering, design, and manufacturing teams to work simultaneously, regardless of geography. From what I’ve read, this seamless collaboration reduces delays, prevents miscommunication, and supports faster product development cycles.
A commonly appreciated element is Teamcenter’s customer support. I’ve come across several reviewers who mention prompt, 24/7 assistance and helpful troubleshooting support, particularly during the onboarding and system configuration phases. This strong support presence seems to help offset some of the complexity users encounter when adopting the platform.
Another strength mentioned in reviews is version control and product integration tracking. G2 users often note that the platform makes monitoring revisions and product iterations easy over time. This visibility helps teams ensure traceability and compliance, which are key needs for organizations with rigorous quality assurance requirements.
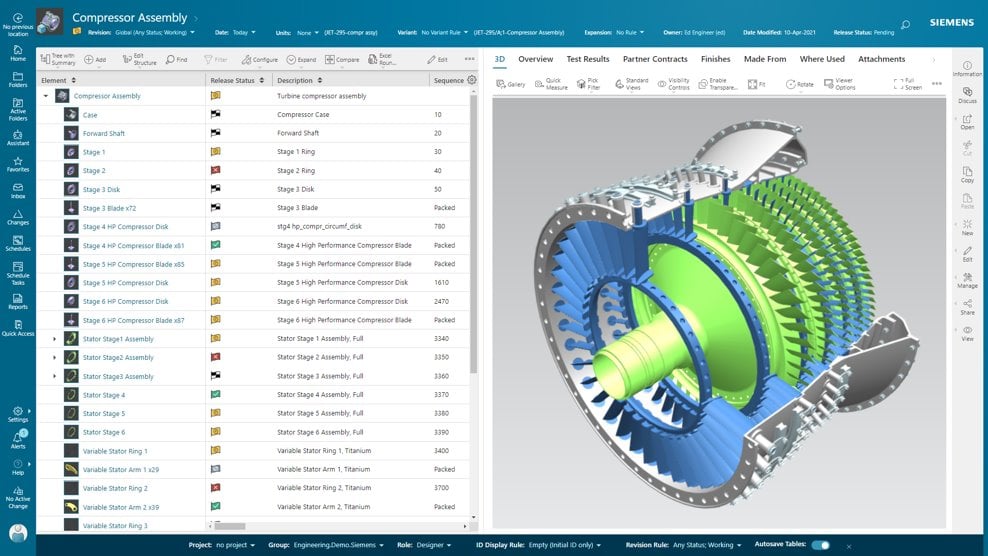
That said, negative feedback tends to focus on the complexity of the platform’s implementation. Some users are frustrated with the time and resources required to configure Teamcenter to match existing workflows. It’s not just an IT lift—multiple reviewers mention that onboarding and training can be steep, especially for teams new to PLM systems.
There’s also noticeable dissatisfaction around performance issues with large datasets. Across several reviews, users mention that Teamcenter can slow down when handling high volumes of historical data or large design files. While it doesn’t completely stop work, it does appear to impact efficiency for teams managing data-intensive projects.
What I like about Siemens Teamcenter:
- I’ve seen G2 users really value Teamcenter’s ability to centralize and manage product data, making it easier to track and retrieve information without relying on scattered spreadsheets.
- From what I’ve read, users appreciate how well it supports real-time collaboration across departments, helping teams avoid delays and work together efficiently.
What G2 users like about Siemens Teamcenter:
"The most important feature I like about Teamcenter is how easy it is to maintain services, especially with their affordable pricing that delivers effective results at a low cost. They also offer the best product data and lifecycle management features."
- Siemens Teamcenter Review, Murl J.
What I dislike about Siemens Teamcenter:
- I’ve come across feedback where users struggle with the complexity of implementation and mention that onboarding can be time-consuming, especially for teams new to PLM tools.
- I’ve noticed G2 reviewers frequently mention slow performance when working with large datasets or complex design files, which impacts productivity.
What G2 users dislike about Siemens Teamcenter:
"If you have large workflows, the interface can be quite slow in updating and displaying information. The query builder is also limited in how complex you can make the search criteria. Since moving to Active Workspace, support expertise seems lacking, and resolving issues takes longer."
- Siemens Teamcenter Review, Brian H.
Explore how ERP solutions can streamline your operations and drive efficiency across your entire business.
2. Arena PLM & QMS
Arena PLM & QMS is widely regarded as a well-structured platform for managing product lifecycle and quality management processes. Users particularly appreciate its ability to streamline operations across multiple departments, making it a good choice for teams looking to integrate their workflows. However, G2 reviewers also mention a few areas where the platform could improve in terms of flexibility and user experience.
One feature that I see getting a lot of praise is Arena's responsive customer support. Many G2 users highlight the quality of technical assistance, often mentioning how quickly the support team responds and how knowledgeable they are in resolving issues. This high level of service seems to ease the learning curve and help users effectively navigate the platform, especially during the initial setup phase.
Something G2 reviewers seem to really appreciate is the platform's flexibility and customization. Multiple users emphasize how Arena allows them to build workflows that match their specific business needs. Whether it's creating approval chains or designing task flows, reviewers consistently note how customizable the system is, making it adaptable to both compliance and operational changes.
One standout capability, according to users, is Arena's modular structure, which organizes workflows into different “worlds” such as Requests, Items, Quality, and Training. This segmentation is frequently praised by reviewers for its simplicity and clarity, as it helps users focus on specific tasks without feeling overwhelmed by unrelated information. Reviewers also appreciate how each "world" includes relevant tools and workflows, making it easy to navigate and use.
Another area where Arena gets high marks is its analytics capabilities. G2 users often mention how easy it is to track key metrics and create dashboards, enabling real-time project monitoring. This visibility allows teams to identify bottlenecks early and make data-driven decisions, keeping projects on track and teams aligned.
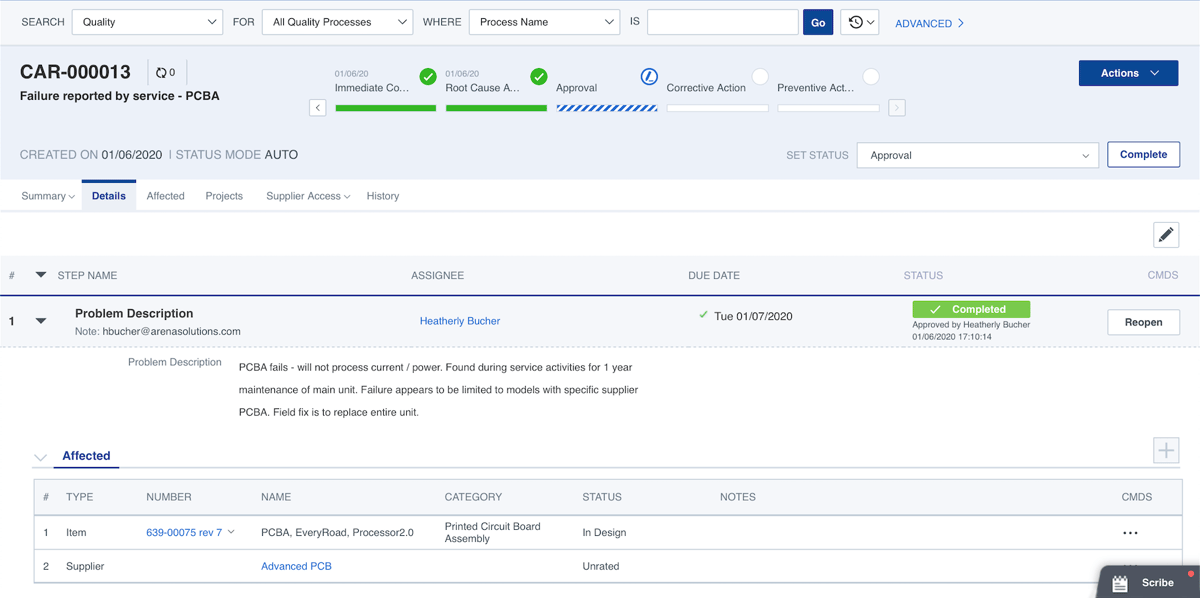
However, negative feedback tends to focus on limitations around data management. Multiple reviewers mention frustration with Arena’s inability to delete or remove items once they're in the production environment. This restriction can lead to a cluttered workspace over time, making it harder to manage data efficiently. Users suggest that features like a “Trash” or temporary holding area would improve the user experience by offering more flexibility.
I’ve come across noticeable dissatisfaction around the import and multi-edit functionalities. Several reviewers point out that while these features are available, they are often seen as clunky and unintuitive. Importing large data sets or applying bulk changes tends to be more cumbersome than expected, leading to additional time or workarounds in order to complete tasks correctly.
What I like about Arena PLM & QMS:
- I’ve seen G2 reviewers consistently praise Arena’s responsive customer support, especially during the initial setup phase, making the learning curve easier to navigate.
- From what I’ve read, users appreciate the platform’s flexibility, allowing them to build customizable workflows that suit their specific business needs.
What G2 users like about Arena PLM & QMS:
"I think Arena QMS can be a game-changer for managing quality and compliance. It’s easy to use and supports many tasks like document control, audit management, and real-time access to information. The cloud-based setup keeps everyone on the team aligned, improving collaboration and efficiency."
- Arena PLM & QMS Review, Moksha M.
What I dislike about Arena PLM & QMS:
- I’ve noticed multiple G2 users express frustration with Arena’s inability to remove items from the production environment, leading to a cluttered workspace over time.
- I’ve come across feedback where users mention that the import and multi-edit features are clunky and unintuitive, making large data management tasks more time-consuming.
What G2 users dislike about Arena PLM & QMS:
"The interface can feel a bit complicated for users, with multiple tabs and conditions. For admins, setup also requires deeper knowledge of the system before they can fully maximize its features."
- Arena PLM & QMS Review, Josefine R.
3. OpenBOM
OpenBOM is frequently praised for its ease of use and modern design, making it especially suitable for small-scale operations that need to manage parts, assemblies, and inventory efficiently. Many users highlight how simple and intuitive the system is, particularly when it comes to organizing and updating bills of materials (BOM). G2 reviewers often mention how quickly they were able to get started without extensive training, appreciating the streamlined navigation that enables them to update part lists with minimal hassle.
A standout feature that I’ve noticed getting frequent positive mentions from G2 users is the ability to attach images to items. This addition is widely praised for improving part identification, as users can quickly reference images instead of relying solely on part numbers or names. This feature, while simple, significantly enhances efficiency for many users, saving time and reducing errors when locating specific parts.
I’ve read multiple reviewers mention how well OpenBOM handles basic inventory management—tracking parts, quantities, and assemblies—all while providing a sleek, cloud-based interface. G2 users appreciate the accessibility it offers, enabling teams in different locations to stay updated in real time. This seems particularly beneficial for smaller businesses that don't require the complexity of a full ERP system.
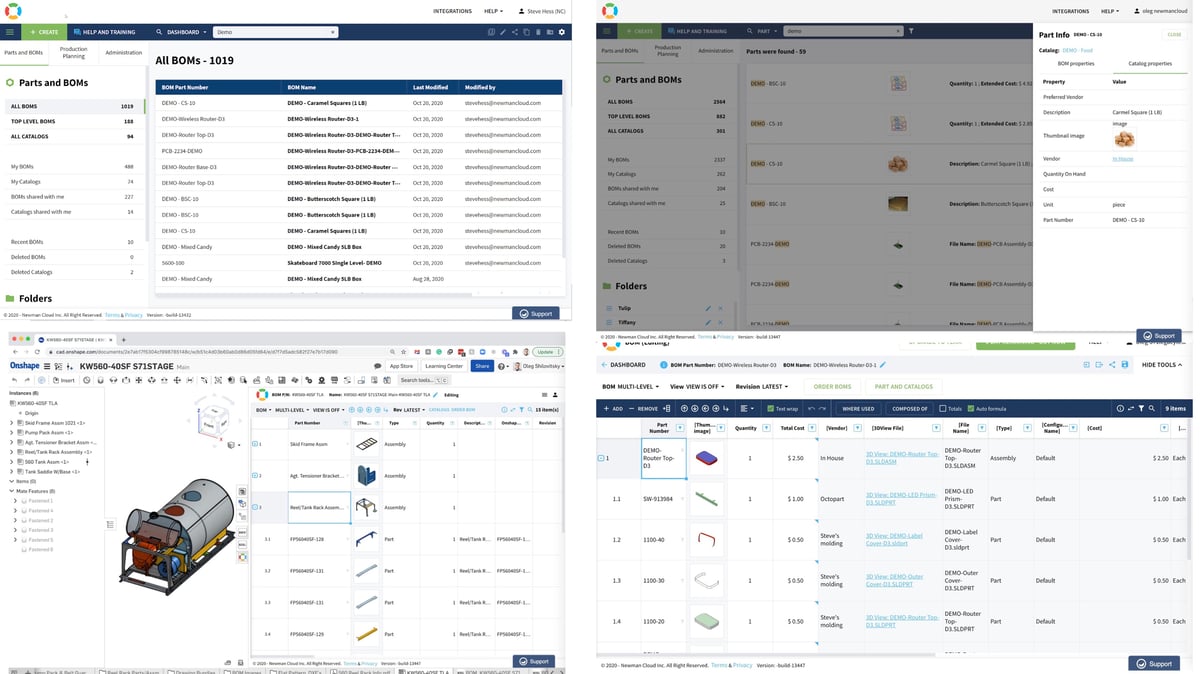
However, workflow guidance is an area where I’ve seen some dissatisfaction. Many G2 users mention frustration with the lack of high-level workflows, particularly when managing production planning and purchase orders. For example, OpenBOM automatically fills in component quantities based on expected needs, but as several users point out, this can be problematic when parts arrive in incomplete shipments. The need to manually adjust quantities and track orders creates an inefficient and error-prone process.
A more significant issue highlighted by users is performance with large files, especially during integration with Solidworks. Multiple reviewers express frustration with OpenBOM crashing when transferring complex or large assembly files, as well as issues with missing STEP or drawing files during the transfer process. These glitches can slow down workflows and require users to retry processes or upload files manually, which detracts from the platform's overall reliability.
What I like about OpenBOM:
- I’ve seen G2 users frequently praise OpenBOM for its ease of use and modern design, particularly how simple it is to organize and update bills of materials (BOM) without requiring extensive training.
- A standout feature I’ve come across in reviews is the ability to attach images to items, which improves part identification and saves users time by reducing errors when locating specific parts.
What G2 users like about OpenBOM:
"OpenBOM allows my team to easily share files, keep them organized, and reuse them across multiple team members. It helps us manage large team files so we can find and use them when needed. The cloud updating feature is especially helpful, letting us lock a CAD part while someone is working on it and reopen it once they’ve finished and updated the part."
- OpenBOM Review, Joshua Y.
What I dislike about OpenBOM:
- I’ve noticed frustration with OpenBOM’s lack of high-level workflows, especially around production planning and purchase orders. This leads to inefficient manual adjustments when parts arrive in incomplete shipments.
- I’ve seen several reviewers express dissatisfaction with OpenBOM’s performance when handling large files, especially during integration with Solidworks. The system crashes or fails to transfer complex files properly, disrupting workflows and requiring users to retry.
What G2 users dislike about OpenBOM:
"Getting started was slow, as it took my MEs a long time to figure out how to structure their SolidWorks files to work with the OpenBOM upload. We've also had issues collaborating on the OpenBOM website and syncing with the ME work. The distinction between items and BOMs can be confusing.
- OpenBOM Review, Josh K.
Explore cutting-edge 3D modeling tools that transform your design process and bring your ideas to life.
4. Onshape
Onshape is often described as a modern, cloud-based CAD platform that brings many benefits, especially for collaborative design. A common theme in reviews is its cloud-based architecture and modern interface, which many G2 users highlight as a significant advantage. Users appreciate that it eliminates the need for heavy software installations and file version conflicts, making it easy to access and work on designs from anywhere. The platform's ability to provide a collaborative environment where teams can work in real-time is frequently praised, as it simplifies sharing and editing designs.
From what I’ve seen, one feature that consistently stands out in G2 reviews is Onshape's built-in version and change control system. Many users express appreciation for this core functionality, which eliminates the need for separate PDM systems and manual backups. The automatic tracking of every edit, branch, and merge seems to improve collaboration, reduce errors, and enhance the overall user experience. It also helps streamline product development, especially when integrated with Arena, PTC’s product lifecycle management system.
A notable strength that G2 users regularly mention is Onshape's frequent updates. Reviewers often highlight the platform’s quick evolution, with significant updates delivered every few weeks. Users seem to appreciate that these updates are not just bug fixes but often introduce new features that improve modeling, usability, and performance. This consistent stream of improvements contributes to Onshape’s reputation as a cutting-edge tool in the CAD space.
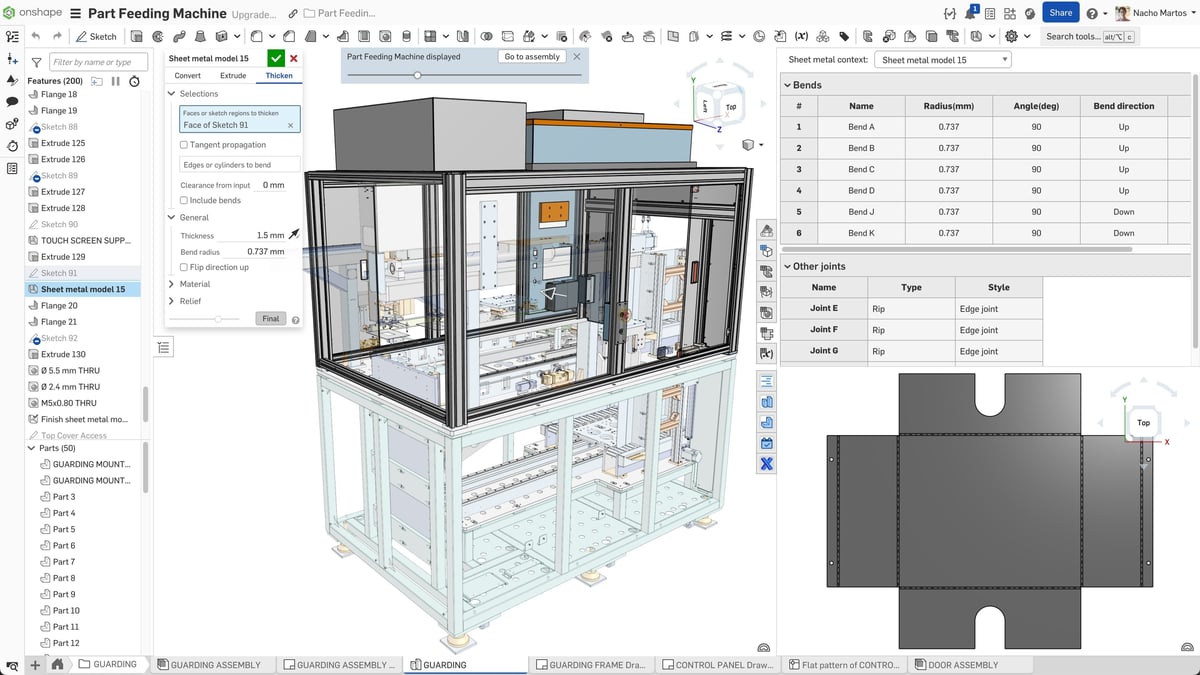
However, I’ve also noticed that G2 reviewers sometimes mention limitations in sheet metal modeling and documentation. Compared to more mature CAD platforms, some users feel that Onshape lacks the advanced features required for handling complex sheet metal projects. As a result, many users have mentioned using workarounds or exporting designs to other tools for final processing, which disrupts their workflows.
In addition, several G2 users have expressed frustration with applying partial surface details like labels, stickers, or logos within assemblies. Reviews point out that there’s no straightforward way to place these details directly on partial surfaces. Users often have to resort to imprints or the Render Studio, which may not be ideal for quick visualizations. This limitation has left some users wishing for more flexible options, especially when working on presentations or visual demos for stakeholders.
What I like about Onshape:
- I’ve noticed that G2 users appreciate Onshape’s cloud-based architecture, which allows easy access to designs from anywhere and eliminates file version conflicts.
- Based on user feedback, Onshape’s built-in version control system is widely praised for improving collaboration by automatically tracking every edit, branch, and merge.
What G2 users like about Onshape:
"It's hard to pick a favorite, but some highlights are the Git-like versioning and history that give ultimate control over every move, the inbuilt FeatureScript language that makes creating custom features super effective, and the browser-based access that lets me work from anywhere, even an internet café or my phone."
- Onshape Review, Christopher D.
What I dislike about Onshape:
- I’ve seen users express frustration with Onshape’s limitations in sheet metal modeling, often relying on workarounds or exporting designs to other tools for processing.
- I’ve come across feedback indicating that applying partial surface details like logos or stickers in assemblies is cumbersome, with no direct method for placing them on partial surfaces.
What G2 users dislike about Onshape:
"The biggest issue I’ve had with Onshape is the assembly build and edit option, which feels less intuitive compared to other CAD tools I’ve used, but I’m gradually getting it figured out."
- Onshape Review, Russell W.
5. Propel
I’ve found that Propel stands out for its impressive customization capabilities, a feature that many users praise. Reviewers consistently highlight this as a key strength, noting that the platform’s ability to be tailored to meet unique business requirements gives it a distinct edge over other solutions. This level of customization allows organizations to design process flows that align precisely with operational needs, ensuring they can adapt the platform to their specific use cases without compromising on functionality.
One of the primary reasons users appreciate Propel’s flexibility in creating workflows is the ability it offers to modify processes according to business needs. Users have mentioned that being able to tailor workflows helps teams collaborate more efficiently, designing processes that are specific to their objectives. This customization helps remove bottlenecks, optimize daily tasks, and improve overall team collaboration, making the platform highly effective for streamlining operations.
In addition to improving team collaboration, Propel’s adaptability is frequently cited as a significant advantage when it comes to boosting operational efficiency. Users report that this high degree of customization enables them to tailor their operations more effectively, leading to better alignment with company goals and a smoother workflow. Ultimately, this results in more organized daily operations, helping businesses meet their goals with greater ease while reducing the friction that comes with using more rigid platforms.
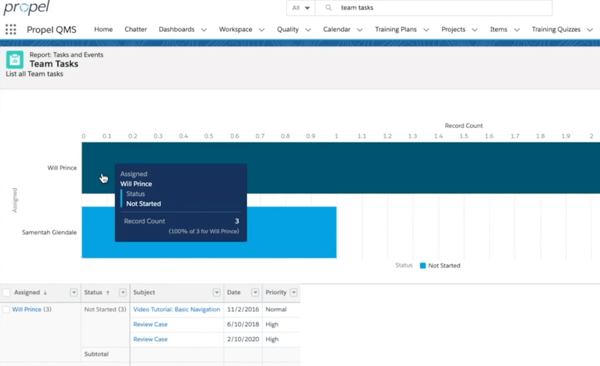
However, I’ve noticed that some users on G2 express frustration with auditability, particularly around file deletions. Many reviewers mention the lack of an audit trail when files are deleted, which creates a gap in accountability. Users, especially those inheriting systems, have emphasized the importance of tracking who deleted files and when, as this is critical in maintaining documentation integrity. This seems to be a recurring issue for those in industries where detailed records are essential.
Another point that comes up in reviews is email notification control. While Propel offers automation for certain processes, multiple G2 reviewers have noted the lack of customization options for email notifications. Users frequently mention that they are unable to adjust the content of notifications or add external recipients, which can lead to important updates not reaching the right people in the right format. This is often seen as an area that needs improvement to enhance communication across teams.
From what I’ve seen in G2 reviews, there’s also some feedback regarding the platform's learning curve. While Propel is known for its flexibility, many users point out that it can be overwhelming for those who are new to the system. Users need a deeper understanding of its structure to fully take advantage of its customization options, which can require significant time and effort. This steep learning curve is often cited by users as a barrier, particularly when it comes to customizing the front-end interface.
What I like about Propel:
- I’ve noticed that G2 users appreciate Propel’s strong customization capabilities, especially the ability to tailor workflows to meet specific business needs, which enhances operational efficiency.
- Based on feedback, users highlight Propel’s flexibility in adapting to unique business requirements, helping teams achieve their goals with greater ease and improving collaboration.
What G2 users like about Propel:
"I must say that what I love about Propel is how it makes managing the product lifecycle easy. When everything is mapped out, we never lose track of a product's development stage. It's a big plus to have a tool that gives us transparency across teams when alignment is needed. One of the best parts is how easily it lets us share updates and feedback, helping us avoid confusion."
- Propel Review, Mark P.
What I dislike about Propel:
- I’ve seen some G2 reviewers express frustration with the lack of an audit trail for file deletions, which they feel compromises accountability and documentation integrity.
- From what I’ve read, several users mention that Propel’s email notification control is limited, as customization options for notification content and external recipients are not available, affecting team communication.
What G2 users dislike about Propel:
"New users would benefit from complete onboarding materials because the learning process requires substantial effort. The customer support team responds slowly to requests during times of high volume operations, which creates frustration for users with urgent problems. The mobile application also requires better functionality along with an enhanced user experience."
- Propel Review, Mark H.
6. Duro
Duro is frequently described as a lightweight, easy-to-use PLM tool that simplifies the process of scaling engineering operations. Many users appreciate its user-friendly interface, which doesn’t overwhelm with unnecessary features. This makes it an ideal choice for organizations just starting to implement product lifecycle management systems. G2 reviewers often highlight how the platform’s simplicity and ease of use make it accessible without a steep learning curve.
One feature that G2 reviewers seem to really appreciate is Duro’s MPN auto-match feature for electronic engineering items. Users consistently call out this automation as a major time-saver, particularly for large parts inventories. The feature automatically matches manufacturer part numbers with corresponding items in the system, reducing manual searches and improving accuracy. This function is often praised for allowing teams to focus on more strategic tasks rather than getting bogged down by repetitive data entry.
Another commonly appreciated element, according to feedback I gathered from G2 users, is the integration transparency included in the enterprise plan. Unlike many other PLM tools that charge extra for integrations or leave users to figure out how to connect different software tools, Duro includes these integrations as part of the plan. G2 reviewers often mention how this transparency eliminates the hassle of hidden costs or complicated integrations, making it easier to streamline workflows across systems.
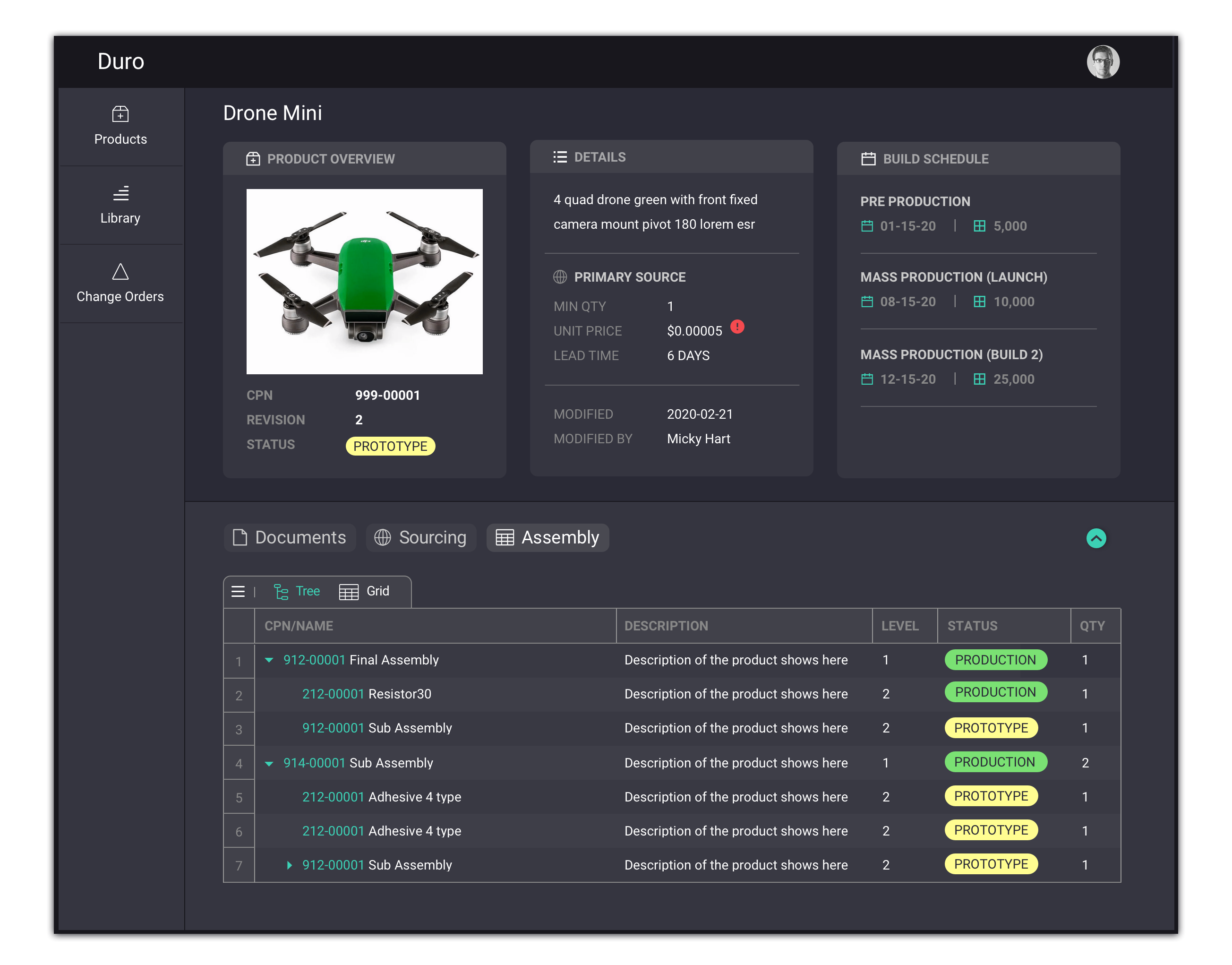
However, G2 users also point out some areas where Duro could improve. One recurring issue is the lack of currency conversion options. According to multiple reviewers, the platform only supports pricing in USD, which can lead to inaccuracies when managing costs for international products. For global organizations dealing with suppliers and customers in different currencies, having the option to convert and select different currencies would be a significant improvement.
I’ve also seen some users express frustration with interface quirks, such as material labels being obscured despite available page space. While not a dealbreaker, several G2 reviewers have mentioned that this small issue caused occasional confusion when trying to access specific material information quickly.
Finally, a limitation that G2 users often mention is the absence of an import feature for vendor mechanical parts. Reviewers point out that this adds manual work when entering data for mechanical parts, especially when importing directly from suppliers. Many suggest that having this feature would streamline workflows and improve efficiency across different parts categories.
What I like about Duro:
- I’ve noticed G2 users consistently highlight Duro’s user-friendly interface and simplicity, making it an ideal choice for teams just starting to implement PLM systems.
- From my review of G2 feedback, the MPN auto-match feature for electronic engineering items is praised for saving time and reducing manual data entry, improving overall accuracy.
What G2 users like about Duro:
"Duro has really simplified our BOM management. Gone are the days of spreadsheets, tedious and error-prone manual entry and updating, and confusion. Now our design engineers can focus on the design work and let Duro handle the handoff of fabrication data to our supply chain team quickly and pain-free!"
- Duro Review, Jesse G.
What I dislike about Duro:
- I’ve seen recurring feedback about the lack of currency conversion options, which limits global organizations dealing with multiple currencies.
- I’ve come across users mentioning frustration with interface quirks, such as material labels being obscured, which can cause confusion during quick access.
What G2 users dislike about Duro:
"Some cons include occasional authentication issues with the Onshape plugin, and the features that would distinguish Duro as a true PLM product (as opposed to just PDM) do not yet seem mature enough to merit their use. I would love to one day use Duro to manage builds, component inventories, and more—it will be interesting to see how their product evolves in the future."
- Duro Review, Tyler B.
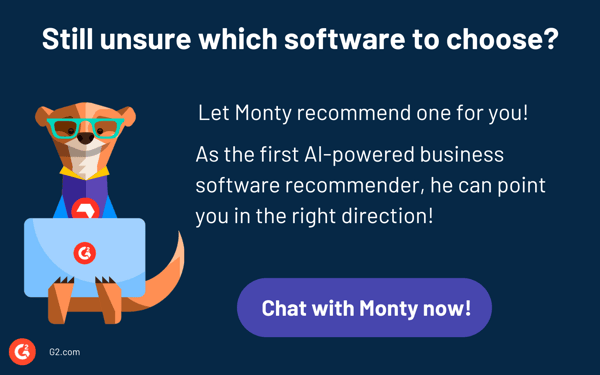
PLM software: Frequently asked questions (FAQs)
1. Which PLM software is ideal for large enterprises?
Siemens Teamcenter is popular among large enterprises for its scalability, advanced integration capabilities, robust collaboration tools, and support for complex product structures.
2. Which is the best PLM software for small businesses or startups?
OpenBOM offers affordable, cloud-native PLM solutions designed for small to mid-sized companies. This includes essential product data management and collaboration features without the heavy complexity.
3. Can PLM software integrate with CAD and ERP systems?
Yes. Most modern PLM solutions offer seamless integration with CAD tools like SolidWorks, AutoCAD, and CATIA, as well as ERP systems like SAP and Oracle to ensure smooth data flow across product development and business operations.
4. What is the difference between PDM and PLM software?
Product data management (PDM) focuses mainly on managing CAD files and technical documentation, while product lifecycle management (PLM) covers the entire lifecycle of a product, from concept and design to manufacturing, service, and disposal.
5. Is cloud-based PLM better than on-premises PLM?
Cloud-based PLM offers advantages like easier updates, lower upfront costs, faster deployment, and accessibility from anywhere. However, some companies with strict data control needs may prefer on-premises solutions.
Precision down to a ‘T’
After thoroughly evaluating the best PLM software, I’ve come to appreciate how much the right system can streamline product development and lifecycle management.
Each platform offers unique features tailored to different needs, whether you’re focused on collaboration across teams, managing complex product data, or accelerating time-to-market. With so many options available, there’s always a solution that can help you manage your product lifecycle more efficiently.
I hope my insights help you find the best PLM software for your organization—because, let’s face it, managing products manually just slows innovation down!
Explore innovative 3D printing solutions that accelerate your prototyping, production, and product development processes.