On a scorching summer day, the office AC broke down. The maintenance team scrambled to find the issue, but without a proper tracking system, they had no record of past repairs or replaced parts.
As a result, it took hours to fix, and in the meantime, productivity plummeted, and everyone struggled in the heat. That got me thinking—how do maintenance teams, facility managers, and manufacturers handling far more critical equipment deal with unexpected breakdowns?
That’s when I started exploring computerized maintenance management system (CMMS) software.
I explored G2 reviews, researched various platforms, and evaluated G2 reviews for different CMMS tools to understand their impact. I found that these systems go beyond simple tracking—they optimize asset performance, reduce downtime, and improve overall efficiency.
If you're searching for the best CMMS software solutions, keep reading. I’m sharing insights from my evaluation experience to help you find the right tool for your needs.
10 best CMMS software: My picks for 2025
- MaintainX for easy setup of work orders and asset management ($16/user/mo)
- Fiix CMMS for AI-powered maintenance automation and analytics ($45/user/mo)
- Limble for user-friendly interface and customizable workflows ($69/user/mo)
- UpKeep for mobile-first capabilities, ease of use, and cloud-based accessibility ($20/user/mo)
- eMaint CMMS for scalability, reporting, and compliance features ($69/user/mo)
- Accruent Maintenance Connection for enterprise-grade asset lifecycle management ($1325/user/year)
- Fracttal One for AI-driven predictive maintenance and IoT integration (available on request)
- Corrigo for vendor coordination and facilities management (available on request)
- eWorkOrders CMMS for strong preventive maintenance capabilities (available on request)
- Click Maint CMMS for simplified maintenance tracking and scheduling ($35/user/mo)
* These CMMS tools are top-rated in their category, according to G2 Grid Reports. I’ve also added their monthly pricing to make comparisons easier for you.
My top 10 best CMMS software recommendations for 2025
Best CMMS software is designed to help businesses efficiently track, maintain, and optimize their assets. While exploring these tools, I saw how they simplify maintenance management, reduce unexpected downtime, and improve overall equipment reliability.
Features like automated maintenance scheduling, real-time work order tracking, and predictive insights help businesses avoid equipment failures instead of constantly reacting to them. I could see how the best CMMS software did all of that and more.
How did I find and evaluate the best CMMS software?
I evaluated reviews for the best CMMS software extensively to understand how they manage and track maintenance tasks, automate work orders, and optimize asset performance.
I used AI to analyze user feedback and reviews on G2 and G2’s Grid Reports to gain further insights into each tool’s features, ease of use, and overall value. The screenshots featured in this article may be a mix of those captured during evaluations and ones obtained from the vendor’s G2 page.
By combining evaluations from expert feedback and user reviews, I’ve compiled a list of the best CMMS software to help you select the right one for your maintenance operations.
What makes CMMS software worth it: My opinion
When evaluating the best CMMS software, I focus on several key features to determine its effectiveness for IT and maintenance teams:
- Asset tracking and management: A CMMS should function as a centralized asset database, providing real-time visibility into equipment, machinery, and facilities. I evaluate how easily users can input asset data manually or via bulk import (CSV, API integration). Searchability is crucial, so I evaluated whether assets can be found using filters like asset type, location, serial number, or maintenance status. I also check for barcode and RFID scanning capabilities, which speed up asset identification. A well-designed CMMS should allow users to attach technical documents (PDFs, images, CAD drawings), warranty details, and IoT sensor data to each asset record for comprehensive tracking.
- Preventive maintenance scheduling: Automation in preventive maintenance ensures that equipment gets serviced before failures occur. I assess whether the CMMS allows scheduling based on time intervals (e.g., every 30 days), usage (e.g., after 500 machine hours), or condition-based triggers (e.g., temperature exceeding 80°C). I also check for built-in workflow automation—can it automatically generate work orders when a maintenance task is due? The best CMMS solutions integrate with IoT-enabled sensors to capture live equipment data and trigger maintenance alerts dynamically.
- Work order management and tracking: Work orders should be easy to create, assign, and update in real-time. I evaluate whether users can generate work orders manually or through automated triggers (e.g., an equipment fault detected by a sensor). A CMMS should support multi-user collaboration, allowing technicians to update job progress, attach images, log used spare parts, and enter detailed issue notes. I also evaluated mobile accessibility—can technicians access work orders from a smartphone or tablet while on-site? Advanced systems support role-based access control (RBAC), ensuring that only authorized personnel can modify critical work orders.
- Inventory and spare parts management: A well-integrated CMMS should track spare parts usage and stock levels, preventing downtime due to missing components. I evaluated whether the software provides real-time inventory updates, automatic reorder notifications, and integration with ERP or procurement systems. A good CMMS should support batch tracking, part serial number identification, and supplier management to streamline procurement. I also check whether it calculates lead times to ensure that essential parts arrive before stock runs out.
- Data-driven insights and reporting: A CMMS should transform raw maintenance data into actionable insights. I assess reporting tools for key performance indicators (KPIs) like Mean Time Between Failures (MTBF), Mean Time to Repair (MTTR), asset utilization rates, and technician efficiency. The best systems provide customizable dashboards with interactive visualizations (charts, heatmaps) and exportable reports (PDF, Excel, or JSON for API-based integrations). Predictive analytics is another valuable feature—some CMMS tools use AI and ML models to analyze historical data and forecast equipment failures before they happen.
- Compliance and audit readiness: Many industries require strict compliance with safety and maintenance regulations. I check whether the CMMS maintains a digital audit trail of maintenance activities, complete with timestamps, user logs, and digital signatures. Automated compliance tracking should cover industry standards like ISO 55000 (asset management), OSHA (safety regulations), or FDA 21 CFR Part 11 (electronic records). I also verify whether the software allows secure document storage for certifications, warranty records, and safety checklists, ensuring everything is accessible during audits.
By evaluating these technical aspects, I can determine whether a CMMS truly enhances maintenance operations or if it lacks the automation and integration necessary for modern IT and facility management teams.
- Manage various types of assets and equipment across multiple locations
- Track inventory for spare parts and materials needed for maintenance
- Schedule maintenance activities such as inspections, repairs, and upgrades
- Manage resources (human and equipment) and allocate them to maintenance operations
- Deliver reports on asset utilization, maintenance costs, and technician productivity
- Ensure asset compliance with safety and environmental regulations
- Provide a mobile-friendly interface or mobile apps for field service technicians
This data has been pulled from G2 in 2025. Some reviews have been edited for clarity.
1. MaintainX
Based on my review of G2 user feedback, MaintainX is a cloud-based Computerized Maintenance Management System (CMMS) designed to streamline maintenance operations for businesses. It helps manage asset performance, work orders, and maintenance tasks, and is particularly appealing to professionals transitioning from spreadsheets.
One standout feature that I see getting a lot of praise is automated asset management. From what I’ve seen, G2 users frequently highlight how this functionality seamlessly connects work orders to the respective assets. Unlike outdated Excel-based systems, it automatically logs every maintenance action, creating a clear, searchable history. This helps eliminate the hassle of manual record-keeping and provides users with reliable, organized data.
The procedures feature is also often mentioned positively in G2 reviews. Users seem to appreciate how intuitive and adaptable it is. I’ve noticed that this feature isn't just limited to maintenance tasks but can be used to support various workflows, which makes it more versatile than users initially expect.
Another frequently praised capability is the meter tracking system. Multiple reviewers mention how this feature provides immediate insights into asset performance, allowing users to catch potential issues before they lead to costly breakdowns. Given the importance of preventive maintenance, this tool seems particularly valuable to businesses aiming to reduce unplanned downtime.
From what I’ve gathered in G2 reviews, MaintainX is generally regarded as a robust and flexible tool. Customization options are a major benefit, enabling users to tailor the system to their needs. However, I’ve noticed some concerns about the risk of incorrect data entry when the system is heavily customized. Based on feedback, more control over user permissions could help mitigate this issue by ensuring more accurate modifications.
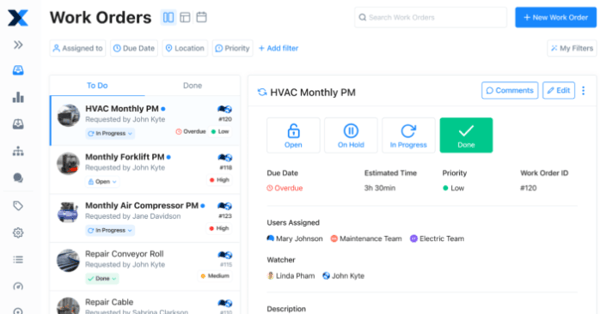
On the downside, G2 users often call out challenges with onboarding and learning the system. While MaintainX offers a wide range of features, some users mention that the system can feel overwhelming at first. I’ve read multiple reviewers suggest that new users could benefit from additional onboarding resources, such as tutorials or tips, to ease the learning curve and help them get up to speed more efficiently.
One area that could benefit from improvement, according to G2 user feedback, is the QR code functionality. While it serves its basic purpose, many users have expressed dissatisfaction with the current labels, which are too basic and lack essential information like asset descriptions and locations. Based on what I’ve seen, the ability to print QR labels in bulk and include more detailed information could significantly improve asset management and operational efficiency.
In summary, G2 reviews generally highlight MaintainX's strong asset management, versatile workflows, and valuable features for preventive maintenance. However, the product's complexity and the need for improved QR code functionality and onboarding support are areas where users have indicated there is room for improvement.
What I like about MaintainX:
- One standout capability, according to users, is MaintainX’s automated asset management, which links work orders to assets automatically, building a searchable history without manual effort.
- I’ve seen G2 reviewers highlight the intuitive procedures feature, noting how it’s easy to adapt beyond maintenance tasks, making the system more versatile than expected.
What G2 users like about MaintainX:
"With MaintainX, we store all our operational procedures, assets, parts, repair records, preventive maintenance plans, and training documents in one place. This has significantly reduced the time our teams spend on communication and tracking repair statuses. It also helps us schedule recurring maintenance and efficiently assign work orders."
- MaintainX Review, John W.
What I dislike about MaintainX:
- While the high level of customization is appreciated, I’ve noticed G2 reviewers point out that it can lead to incorrect data entry if users aren’t careful.
- Based on user feedback, the feature set can feel overwhelming at first, with several reviewers mentioning it took time to get comfortable and that new users might need more onboarding support.
What G2 users dislike about MaintainX:
"The only change I would make to MaintainX is the ability to customize the specific permissions of each full user in the system. "
- MaintainX Review, Joseph M.
2. Fiix CMMS
Based on my review of G2 user feedback, Fiix CMMS is a cloud-based tool praised for its accessibility, scalability, and cost-effectiveness. Users appreciate its reduced IT requirements, automatic updates, and the ability to seamlessly analyze maintenance data through artificial intelligence. One standout feature that I’ve noticed getting a lot of praise is the system’s ease of implementation. G2 reviewers commonly mention how smoothly the transition from paper-based systems went, and how intuitive the training process was, allowing users to quickly get everything up and running without complications.
A consistent theme in G2 reviews that I’ve noticed is Fiix’s data analytics capabilities. Many users highlight how easy it is to store and analyze historical maintenance data, identifying trends and tracking maintenance indicators in ways that are more seamless compared to other systems. This data-driven approach to maintenance planning is highly valued by users, particularly those looking to optimize their operations.
One feature that stands out in reviews is Fiix’s connectivity, particularly its ability to integrate with programmable logic controllers (PLC) for real-time data collection and automated machine responses. G2 users frequently highlight the system’s integration with integrated plant systems (IPS), centralizing operations and improving overall efficiency. Additionally, the predictive maintenance tools and vibration analysis integration are frequently praised for their ability to detect mechanical issues early and anticipate equipment failures, which are seen as incredibly valuable tools for maintenance teams.
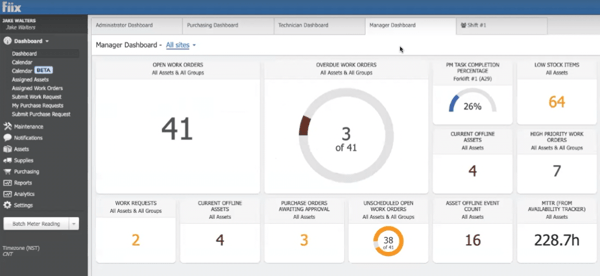
However, across multiple reviews, I’ve noticed users expressing concerns about the system’s flexibility in terms of managing schedules. While Fiix offers a solid foundation for schedule management, the lack of customization options seems to be a recurring issue for teams with dynamic maintenance needs that require frequent adjustments. G2 reviewers suggest that more flexibility in this area would significantly improve the overall experience.
In terms of mobile accessibility, G2 users frequently note the mobile app’s helpfulness for teams on the go, but I’ve also come across feedback mentioning minor usability issues. Some users find that the Android and iOS versions don’t align perfectly in terms of features and functionality, which can be frustrating for teams using different devices.
Finally, I’ve seen some users mention issues with language translations within Fiix. While the system is growing, a few users expressed frustration with incomplete or inconsistent translations, which could confuse multilingual teams. As one reviewer put it, the mix of languages in certain areas could be a barrier to teams that rely on precise instructions in their preferred language. Hopefully, as the system continues to evolve, these translation issues will be addressed to improve the experience for diverse user bases.
What I like about Fiix CMMS:
- I’ve read G2 reviews highlighting that implementing Fiix CMMS was surprisingly smooth, with users noting a quick transition from paper-based systems and intuitive training that got them up and running fast.
- One feature that gets a lot of praise is the historical data record, which many users found helpful for tracking maintenance trends and using analytics tools to make data-driven decisions.
What G2 users like about Fiix CMMS:
"Fiix is an easy-to-use and intuitive tool for managing projects and tasks within companies. It offers robust reporting and data analysis features, making it a great software solution. Additionally, Fiix provides helpful instructions to assist new users in navigating the application. It is a user-friendly tool for various industries, and one of its biggest advantages is its excellent customer support."
- Fiix CMMS Review, Weronika R.
What I dislike about Fiix CMMS:
- I’ve noticed G2 users often highlight the centralized scheduling as a helpful part of the work order management system, though some feel it's not flexible enough for teams with evolving maintenance needs.
- Based on G2 reviews, there’s noticeable dissatisfaction around the mobile app experience, especially due to inconsistent features between Android and iOS versions, which can impact users relying on mobile access.
What G2 users dislike about Fiix CMMS:
"The system lacks an advanced option for creating scheduled maintenance work orders, similar to what is available in the SAP Materials Management (MM) module. It allows duplicate inspection orders without an intelligent check to prevent them. The app does not fully meet expectations, as the Android and Apple versions differ significantly. Some features are not translated into the selected language, leading to information being displayed in English. Additionally, there is no support for the Brazilian currency (reais). The system also does not allow estimated and execution times to be divided into minutes, making it difficult to convert fractional hours accurately."
- Fiix CMMS Review, Guilherme C.
3. Limble
Based on my review of G2 user feedback, Limble is a cloud-based CMMS that is frequently praised for its customizability, making it highly adaptable for industries like manufacturing, healthcare, and facilities management. A common theme in G2 reviews is the system’s flexibility, allowing users to configure custom fields and refine how maintenance tasks are tracked to fit their specific needs. This adaptability is particularly appreciated by teams looking to seamlessly integrate the system into their existing workflows without requiring major adjustments.
The user interface is another feature that receives a lot of positive attention from G2 reviewers. It's described as clean, intuitive, and easy to navigate, which is especially beneficial for those new to CMMS software. From what I’ve seen, users appreciate how simple the setup process is, ensuring a smooth transition and minimizing complications when getting started.
Another standout feature, according to G2 reviews, is the dashboard, which updates every 5 minutes. Users frequently mention how customizable the dashboard is, allowing them to monitor key metrics in real-time and tailor the data to their preferences. Many users find this valuable for tracking performance and gaining insights at a glance, especially in high-pressure environments where quick access to information is crucial.
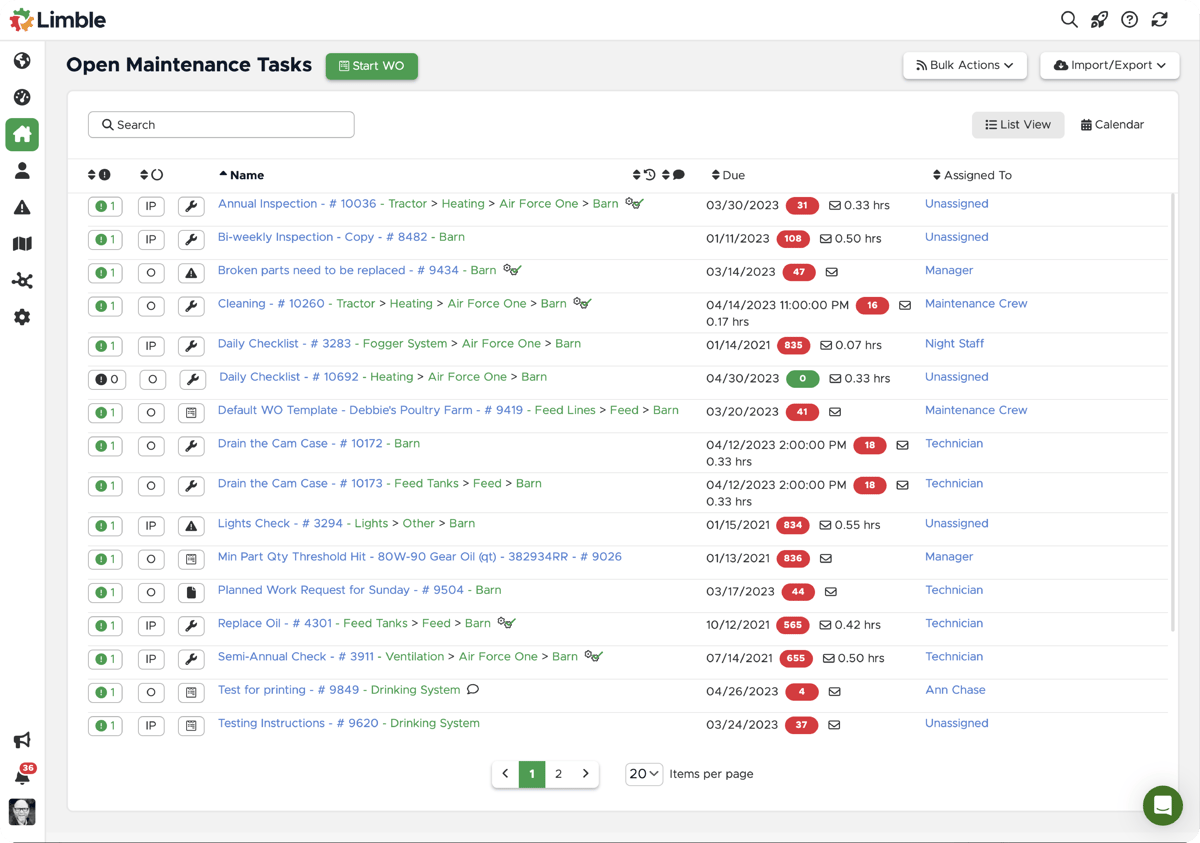
However, based on feedback I’ve gathered from G2 users, there are a few areas where Limble could improve. For instance, many users mention the challenge of setting up customizable dashboard widgets. While the feature itself is useful, G2 reviews indicate that the numerous technical settings and options can feel overwhelming, making it difficult for users to fine-tune the widgets and get the exact data they need.
When it comes to reporting, I've seen multiple users express frustration with the process. While Limble is generally user-friendly, some users find extracting detailed reports from specific datasets difficult. Several reviewers mention that they often have to export data to Excel for further manipulation, which adds an extra step. For users working in high-pressure environments, this extra step can be time-consuming, as they prefer to handle reporting directly within the software to save time.
Finally, the mobile app receives mixed reviews. Although it offers convenience, G2 users note occasional freezing and issues with inaccessible links in the "Manage Work" menu. These glitches can disrupt workflow, and based on feedback, it seems that streamlining the mobile experience to align more closely with the desktop version would greatly enhance reliability and user satisfaction.
What I like about Limble:
- A consistent theme in G2 reviews that I’ve noticed is how customizable Limble is—users appreciate the ability to create custom fields and adjust task tracking to fit their workflows.
- I’ve come across many reviewers who praise the clean and intuitive interface, noting that even users new to CMMS tools find the setup process simple and the transition smooth.
What G2 users like about Limble:
"Limble is simple, powerful, and gets the team excited. The pricing is comparable to previous software but offers more value for our money, plus a free trial to demonstrate how easy it is to use—something no other company (from the demos I've seen) offers. It's a one-stop place to find all the data we need to do our jobs effectively. After reviewing over 12 different CMMS programs, Limble checked all the right boxes, and our team is thrilled to use it every day. Another great thing is the support—Limble has truly excelled in customer service, being available day and night with solutions to even the most unique requests, always answering with "Yes!"
- Limble Review, Alex B.
What I dislike about Limble:
- One feature that I see getting a lot of praise is the customizable dashboard widgets, which let users personalize how they view data—though some G2 reviewers mention setup can be a bit challenging.
- I’ve read multiple reviewers mention struggles with reporting features, noting that while the platform is user-friendly overall, pulling detailed reports from specific datasets isn’t always straightforward.
What G2 users dislike about Limble:
"First, there’s no complete audit trail for task workflows, making it hard to attribute work completion to the correct technician, especially when tasks are assigned to multiple people. Second, metrics like downtime and Mean Time to Repair (MTTR) are only logged once tasks are closed, but some tasks take weeks or months to close, making the data outdated. It would be great if downtime on open tasks could be tracked automatically. Lastly, there’s no good scheduling module, and it’s challenging to manage task scheduling without changing fixed due dates or relying on manual inputs in Excel."
- Limble Review, Verified User in Pharmaceuticals.
Explore inventory control tools that can provide real-time insights into the performance of your asset management processes.
4. UpKeep
Based on my review of G2 user feedback, UpKeep is a highly regarded mobile-first, fully featured CMMS designed to enhance maintenance management. A consistently praised feature is its intuitive design, which allows both technicians and requesters to be onboarded quickly. G2 users frequently highlight how the system’s simplicity and ease of navigation enable new users to rapidly learn how to create and manage work orders without feeling overwhelmed. This user-friendly interface appears to be one of the standout features for many.
Adoption metrics are another aspect that receives positive feedback from G2 reviewers. The high customizability of this feature allows users to track how well teams are adopting the system and make adjustments as needed. According to feedback, this flexibility is especially appreciated by users who want to monitor progress and improve system engagement within their teams.
Another feature that stands out in reviews is seamless scheduling for both preventive and reactive maintenance. G2 users appreciate how easily they can assign, track, and adjust maintenance tasks, ensuring that no work orders are missed. Reviewers often mention how this feature contributes to smoother operations, especially when tasks can be built and scheduled simultaneously, helping technicians who are new to CMMS software feel more comfortable with the system.
Real-time work order tracking and mobile accessibility are also frequently mentioned in positive reviews. Users enjoy the ability to check work order statuses, update tasks, and communicate with teams on the go. This feature significantly improves maintenance efficiency, and the centralized data storage enhances collaboration by ensuring that all team members have access to the most up-to-date information, reducing miscommunication and delays.
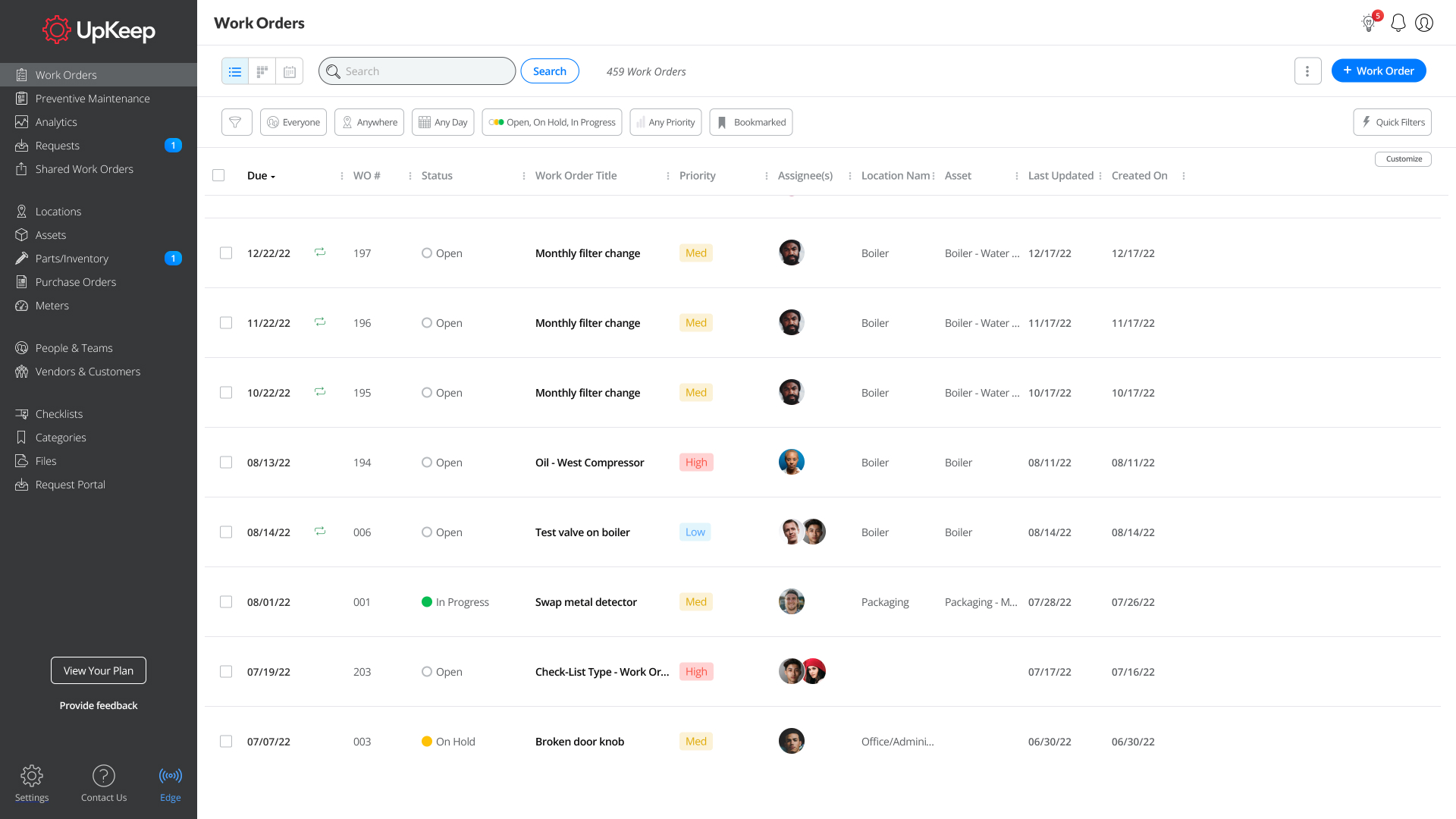
However, from my review of G2 user feedback, I’ve noticed some areas where users have pointed out opportunities for improvement. One common concern is the bulk importing and exporting of work orders, especially for preventive maintenance. G2 reviewers frequently mention that creating multiple PMs at once requires more steps than expected, which can feel like a setback in the process. Despite this, the customizable maintenance schedules are often appreciated, as they allow teams to tailor workflows to meet specific needs.
Many G2 users have also expressed frustration with inventory management integration. Currently, there’s no way to link specific work orders with assets or automatically update inventory when purchase orders are received. This limitation requires additional manual effort to track stock levels, which could be more efficient. That said, the asset management feature does help users track important equipment, ensuring maintenance activities are carried out on the correct assets.
Additionally, I've noticed that some users report occasional glitches when saving quick filters. While these issues aren't overwhelming, they can be inconvenient, leading to reconfiguring filters or losing settings. This seems to be a minor issue, but it’s something G2 reviewers have mentioned as a point of frustration.
What I like about UpKeep:
- I’ve seen many G2 reviewers highlight UpKeep’s intuitive design as a major advantage, making it easy for both technicians and requesters to onboard and manage work orders without much hassle.
- A commonly appreciated element is the adoption metrics feature—from what I’ve read, users value the ability to track system usage and make custom adjustments to boost adoption across teams.
What G2 users like about UpKeep:
"From my perspective in a training role, Diego at Upkeep gave us all the support we needed to get up and running. He took the time to work with various stakeholders, ensuring a proper introduction to the system and a clear understanding. He even joined an employee training call to answer any questions I couldn’t handle. The feedback has been positive—users appreciate how easy the app is to use and how it helps them stay organized, preventing them from losing track. I truly appreciated this level of support for a new system!"
- UpKeep Review, Glenda R.
What I dislike about UpKeep:
- I’ve read multiple G2 reviews pointing out that bulk importing and exporting PM work orders involves extra steps, which can slow down the process and reduce efficiency.
- From what I’ve seen, users express frustration with the inventory management integration, as it doesn’t automatically link work orders to assets or update inventory upon receiving items, requiring more manual work.
What G2 users dislike about UpKeep:
"A few areas for improvement include the PM process for exporting and importing large numbers of Preventive Maintenance tasks, which could be more efficient. Updates should be tested with customer support before being released to customers. More consideration needs to be given to the types of industries using Upkeep, though the platform is improving in this area. Additionally, better customization options for forms are needed."
- UpKeep Review, William C.
5. eMaint CMMS
Based on my review of G2 user feedback, eMaint CMMS is widely praised for its ability to manage work orders, preventive maintenance, scheduling, asset management, spare parts inventory, and condition monitoring with ease. One feature that I frequently see getting a lot of praise is its organized system for tracking preventive maintenance. Many users highlight how this functionality is crucial for minimizing machine downtime and ensuring maintenance tasks are scheduled and monitored efficiently, keeping operations on track.
A commonly appreciated element is centralized asset management, which allows users to attach machine user manuals, work instructions, sign-off forms, and parts check-out details directly to each asset. According to G2 reviews, this centralized approach makes the system highly organized, and users seem to really appreciate how everything they need is stored in one place, reducing the hassle of searching across different platforms or physical records.
From what I’ve seen, the integration with inventory tracking and external systems like oil analysis labs is another feature that gets a lot of positive attention. This seamless connection ensures parts are available when needed, which is crucial for avoiding delays and enhancing the efficiency of maintenance operations. G2 reviewers seem to highlight how well this integration works in practice, contributing to smooth operations and reducing the risk of inventory-related issues.
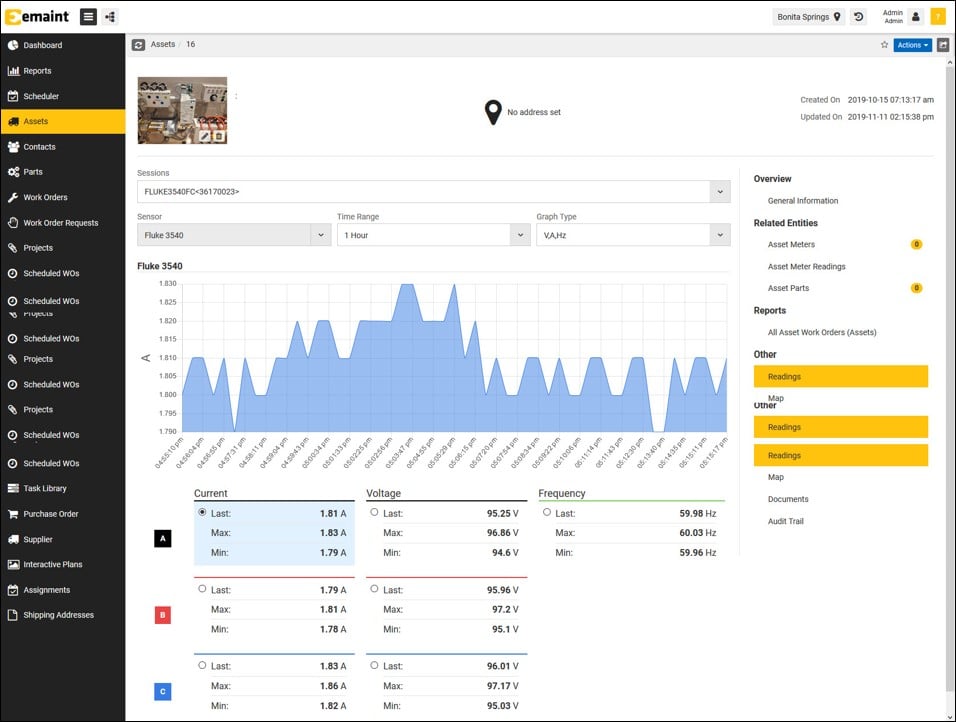
However, negative feedback tends to focus on a few areas where users see room for improvement. One limitation that I've noticed in reviews is the inability to close multiple work orders at once. For those managing a backlog of maintenance tasks, the lack of bulk closure options is a significant time sink. This feature seems to be a common pain point for users looking to improve workflow efficiency.
Another area where some users express dissatisfaction is with the reporting function. While the system provides reports, many G2 users note that the lack of flexibility in output formats can make it difficult to tailor reports to specific needs or present data in a more accessible and user-friendly way for non-technical users. This seems to be a limitation that stands out in reviews, particularly for teams without a technical background.
I’ve also come across noticeable dissatisfaction around advanced reporting capabilities. Multiple G2 reviewers mention how the system’s lack of an intuitive interface for complex reports could be a barrier for users without experience in JSON coding. For these users, generating detailed reports becomes a challenge, which could potentially limit the tool's accessibility for teams that need detailed insights without deep technical expertise.
What I like about eMaint CMMS:
- I frequently see G2 reviewers highlight structured preventive maintenance tracking as a strong point, noting that it helps schedule and monitor tasks efficiently to minimize machine downtime.
- One standout capability, according to users, is the centralized asset management system, which makes it easy to attach manuals, instructions, and part details—streamlining access and reducing the need to toggle between platforms.
What G2 users like about eMaint CMMS:
"eMaint is easy to learn and integrate into your maintenance program. I use it daily to manage assets and create Preventive Maintenance (PM) schedules. It has helped our plant significantly reduce machine downtime by proactively managing PMs. The ability to add machine user manuals, work instructions, sign-off forms, parts check-out, and more for each asset helps keep everything organized in one place. The report-building feature is fantastic for analyzing machine and technician efficiency, and creating custom dashboards with charts and graphs offers a great visual tool. Their support team is always quick to respond and resolve any issues."
- eMaint CMMS Review, Verified User in Manufacturing
What I dislike about eMaint CMMS:
- I’ve come across noticeable dissatisfaction around the lack of a bulk action feature—G2 users mention that not being able to close multiple work orders or delete multiple procedure steps adds time and complexity when managing large workloads.
- Based on my review of G2 feedback, the reporting functionality is another area of concern, with users finding it difficult to customize output formats and noting that advanced reports often require JSON coding knowledge, which not all teams have.
What G2 users dislike about eMaint CMMS:
"The reporting function's output format is limited. X4 could use some format upgrades, though it seems these are being addressed in X5. Additionally, the forms need logic capabilities so that when one item is selected, relevant fields appear. This would help admins guide users more effectively within the system."
- eMaint CMMS Review, Philip A.
6. Accruent Maintenance Connection
Based on my review of G2 user feedback, Accruent Maintenance Connection is praised for its seamless SAP integration for asset parts ordering, which stands out as one of the most appreciated features. Many users on G2 highlight how this integration eliminates the need to manually track parts, making it much easier for maintenance teams to manage inventory without delays. This feature is especially beneficial for businesses already using SAP for procurement, streamlining the entire process.
From what I’ve seen, the asset hierarchy structure is another feature that receives positive attention. This structure aligns well with preventive maintenance reliability concepts, and users seem to appreciate how it allows for automatic addition of preventive maintenance (PM) tasks based on asset class. G2 reviewers frequently highlight how this automation helps keep maintenance schedules dynamically updated, reducing manual intervention and ultimately enhancing equipment reliability.
Mobile accessibility is also frequently mentioned as a strong suit by G2 users. The intuitive mobile interface allows users to track work orders, update maintenance tasks, and manage assets on the go. This functionality is especially valued by technicians working in large facilities who require real-time updates and quick access to critical maintenance information. There’s a lot of love for how this tool handles mobile accessibility, with many reviewers noting its positive impact on productivity.
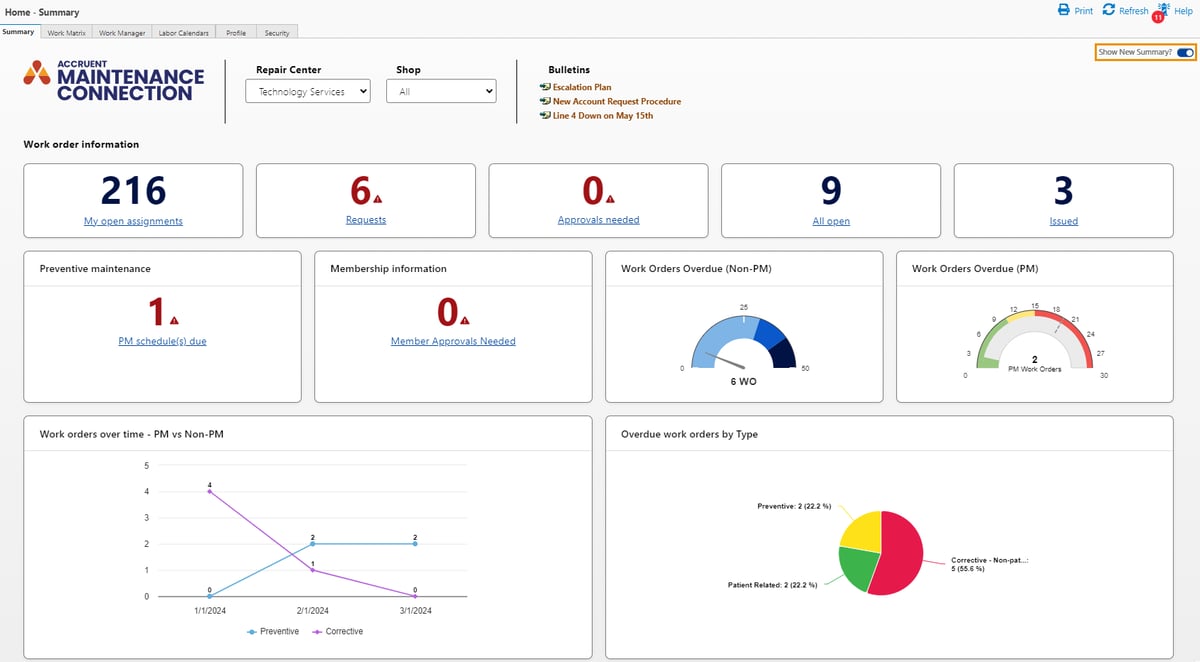
However, looking at the broader review trends, I’ve noticed a few recurring points of dissatisfaction. One challenge that several G2 reviewers call out is the inability to assign multiple cost codes to a single work order. This limitation can be particularly problematic for organizations needing to allocate costs across different departments or budgets, making financial tracking less flexible than expected.
Another commonly mentioned concern is the lack of full customization capabilities for large-scale deployments. While the system performs well with its core tools and modules, G2 users express a desire for more admin control over features such as rules management and report customization. Increased flexibility in these areas would better suit complex organizational needs.
Lastly, there’s noticeable dissatisfaction around inconsistent notification delivery. Some G2 users have reported delays or failures in receiving alerts for work orders and asset updates, which can lead to missed maintenance tasks or scheduling inefficiencies. Improving the reliability of notifications across all devices seems to be a priority for many reviewers to enhance real-time communication within maintenance teams.
What I like about Accruent Maintenance Connection:
- A standout capability, according to G2 reviewers, is the seamless SAP integration for asset parts ordering, which eliminates manual tracking and helps maintenance teams manage inventory efficiently without delays.
- I’ve noticed that G2 users really appreciate the asset hierarchy structure, especially how it aligns with preventive maintenance concepts and automatically adds tasks based on asset class, reducing manual effort and keeping schedules updated.
What G2 users like about Accruent Maintenance Connection:
"The customer service during development and implementation was very responsive. They were willing to collaborate with us as a vendor to tailor the configuration to our needs. The software is intuitive and feature-rich, going beyond just asset management, preventive maintenance, procedures, and task tracking. It even includes a project module for handling group service requests and tracking costs."
- Accruent Maintenance Connection Review, Ron M.
What I dislike about Accruent Maintenance Connection:
- Centralized maintenance data management stands out in G2 reviews, with many users appreciating how it consolidates asset-related information into one place, improving efficiency in tracking and managing operations.
- I’ve seen several G2 reviewers highlight the AI Maintenance Assistant, Tony, as a standout feature, praising its ability to provide instant answers and streamline maintenance processes.
What G2 users dislike about Accruent Maintenance Connection:
"The reporting feature could use an upgrade to save changes once a field is added. I run reports daily and have to keep adjusting the fields, even though I've set them to "year to date."
- Accruent Maintenance Connection Review, Verified User in Machinery
7. Fracttal One
Fracttal One is a CMMS designed to manage comprehensive asset maintenance, and from the feedback I’ve reviewed, users appreciate its dynamic and user-friendly interface, which makes it accessible to both experienced and less-experienced maintenance managers alike.
A centralized maintenance data management system is a standout feature. I’ve noticed that G2 reviewers frequently highlight the benefit of having all maintenance-related information—assets, work orders, spare parts, and performance metrics—in one place. This integration simplifies the tracking and management of operations, reducing the need for multiple systems or spreadsheets and streamlining maintenance processes.
The preventive and predictive maintenance scheduling feature also receives positive feedback from G2 users. Many reviewers praise how the system allows businesses to set up automated maintenance schedules, helping them proactively maintain assets and reduce the risk of unexpected breakdowns. This capability ultimately leads to better asset reliability and performance, a key benefit that’s often mentioned in user reviews.
Another feature that consistently receives praise is the ability to access maintenance records, update work orders, and track spare parts consumption in real-time via mobile devices like smartphones and tablets. Users highlight how this flexibility enables maintenance teams to respond quickly to issues, which is particularly beneficial for teams in the field or those requiring on-the-go management.
One feature that G2 reviewers seem to really appreciate is Tony, the AI Maintenance Assistant. This intelligent virtual assistant enhances productivity by quickly answering maintenance-related queries and helping users complete tasks more efficiently. Multiple users on G2 have praised how this AI-driven functionality speeds up task completion and reduces the need for manual searches.
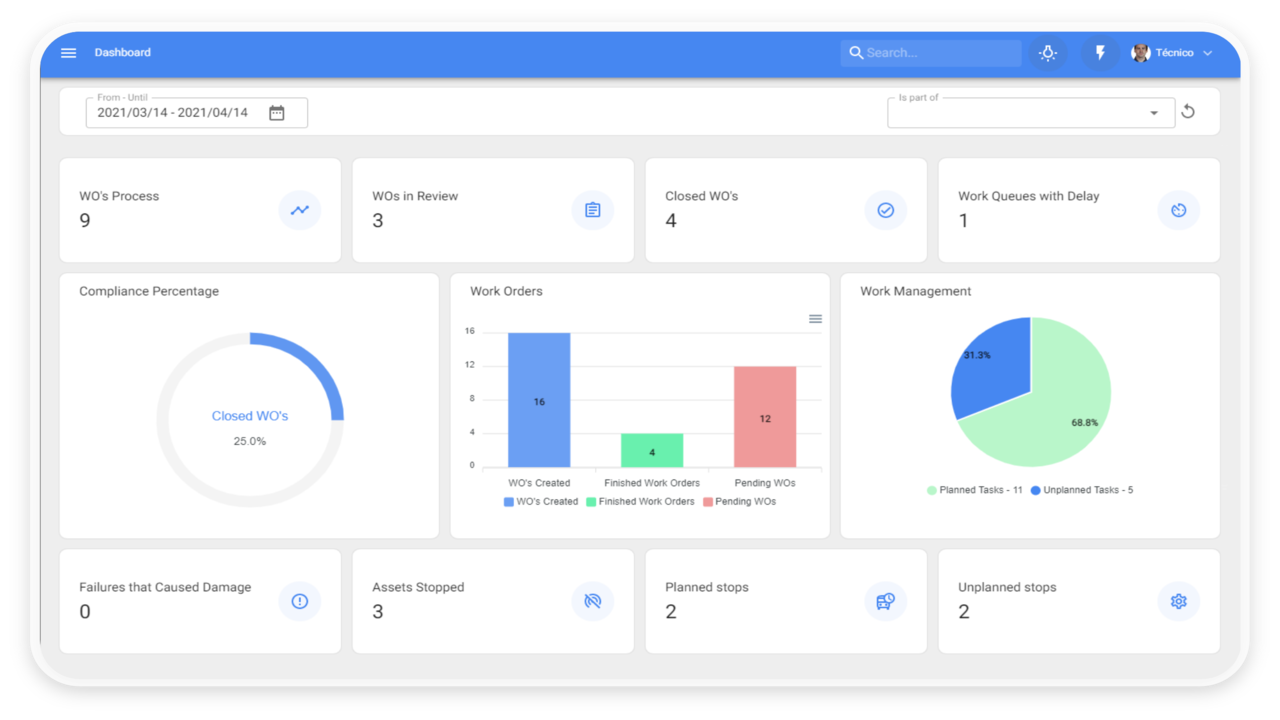
However, from my analysis of G2 reviews, measurement points functionality is one area where users have expressed dissatisfaction. While the system allows for some tracking, many reviewers mention the lack of a dedicated feature for recording and analyzing vibration measurements or electrical parameters in motors. G2 users feel that adding this capability would allow maintenance teams to identify trends and take preventive actions before failures occur.
In terms of platform performance, several G2 reviewers have pointed out slow loading times when the system handles large data volumes. This seems to be a consistent point of frustration for users dealing with extensive maintenance records. Improving the system's performance in this area would enhance the overall user experience, as indicated by several reviewers.
Lastly, I’ve seen G2 users raise concerns about the unidirectional API. Currently, the API only allows the system to receive data from external systems but doesn’t send data back. According to user feedback, having a bidirectional API would significantly improve its functionality, allowing seamless data exchange with ERPs and other business software, thus enhancing its integration capabilities.
What I like about Fracttal One:
- Centralized maintenance data management stands out in G2 reviews, with many users appreciating how it consolidates asset-related information into one place, improving efficiency in tracking and managing operations.
- I’ve seen several G2 reviewers highlight the AI Maintenance Assistant, Tony, as a standout feature, praising its ability to provide instant answers and streamline maintenance processes.
What G2 users like about Fracttal One:
"It is a highly versatile tool for controlling, monitoring, and planning maintenance activities. It enables the integration of personnel, suppliers, customers, equipment, tools, materials, costs, execution times, and frequency. Additionally, it supports the automation of maintenance tasks."
- Fracttal One Review, Heder G.
What I dislike about Fracttal One:
- I’ve noticed that G2 users often mention the measurement points functionality as a limitation, particularly with its lack of advanced tools for tracking vibration or electrical parameters in motors, which impacts predictive maintenance capabilities.
- A common concern raised by reviewers is the unidirectional API integration, which can receive data but cannot send it back, limiting its ability to fully integrate with ERPs and other business systems.
What G2 users dislike about Fracttal One:
"Fracttal One could improve the speed of loading information, as it can sometimes be slow."
- Fracttal One Review, Hosayn R.
8. Corrigo
Corrigo is a comprehensive CMMS designed to help facility managers effectively manage work orders, asset tracking, and vendor relationships at scale. From the G2 reviews I’ve analyzed, users often highlight the platform’s strength in supporting high-volume environments, where managing multiple assets and coordinating maintenance activities is essential.
One feature that stands out in the feedback I’ve reviewed is its ability to capture and organize vast amounts of data. Users consistently praise how the system allows them to store detailed information on physical buildings, equipment assets, and both preventive maintenance (PM) and demand work. G2 reviewers seem to appreciate the ease with which they can manage maintenance schedules and track the status of work orders and assets, which streamlines operations.
Another element that frequently receives positive feedback is customization. Many users highlight the platform’s flexibility, which allows them to tailor it to meet the specific needs of different facilities. Whether adjusting workflows, creating unique asset tracking parameters, or managing various types of maintenance tasks, G2 reviewers often mention that Corrigo enables users to adapt the system to their operational requirements.
From what I’ve seen, G2 users also appreciate Corrigo’s ability to centralize work orders, communication, and invoicing. This unified platform provides businesses with insights into their expenditures and helps identify trends or issues impacting their bottom line. Many users note that having all relevant data in one place simplifies the process of analyzing costs and uncovering inefficiencies, which ultimately improves financial visibility.
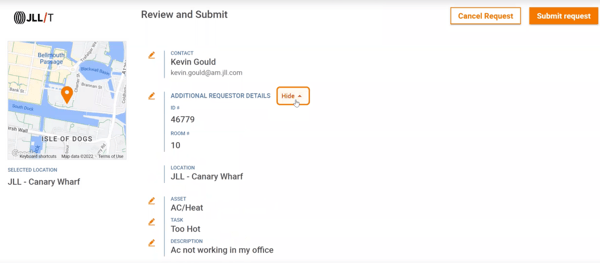
However, I’ve noticed some areas where Corrigo could improve based on user feedback. One challenge I’ve seen mentioned multiple times is the limitation around dual on-call assignments. Currently, the system only allows one technician to be assigned emergency work orders, which some G2 reviewers believe could be more efficient if multiple technicians with different specialties were able to receive such tasks. This feedback is particularly common among users managing diverse, multi-skilled teams who require various areas of expertise for emergency work.
Additionally, I’ve read multiple reviewers mention frustration with custom integrations taking longer to implement than expected. While users note that the integration process improves once it’s underway, many highlight that the initial setup can be slower than anticipated. A faster or more streamlined integration approach would likely improve user experience by helping businesses get up and running with new features or external tools more quickly.
Another common point of dissatisfaction revolves around site-specific customizations. Based on G2 reviews, users often express a desire for more flexibility in applying settings changes at the individual site level. As it stands, adjustments to the system apply across all sites, which can make it difficult for users with unique property configurations to customize the platform to meet specific client or location needs. Allowing users to apply settings on a per-site basis could provide more control and better accommodate the varied requirements of different facilities.
What I like about Corrigo:
- A commonly appreciated element in G2 reviews is the platform’s ability to capture and organize vast amounts of asset data, which makes tracking work orders and asset statuses much more efficient and streamlined for maintenance management.
- Something G2 reviewers seem to really appreciate is Corrigo’s customization capabilities, allowing users to tailor workflows and asset-tracking parameters to meet specific needs, offering flexibility across different facilities.
What G2 users like about Corrigo:
"The response times to inquiries are quick, with seamless capability and knowledge. The thoughtful and inquisitive responses ensure customers get exactly what they need. This site is great for budgeting purposes and identifying areas where you're experiencing the most issues at your facility."
-Corrigo Review, Nicholas P.
What I dislike about Corrigo:
- I’ve seen multiple G2 reviewers mention the dual on-call assignment limitation, noting that the system only supports one technician per emergency work order, and expanding this to include multiple technicians with different specialties would improve efficiency.
- Based on feedback I’ve gathered, custom integrations are often pointed out as taking longer than expected, with users suggesting that a more streamlined implementation process would enhance the overall experience and speed up access to new features.
What G2 users dislike about Corrigo:
"Since the configuration settings are very granular, some can be difficult to find. It's easy to get lost in the numerous tabs and menus. I believe more intuitive categories or a search function for settings could make navigation easier."
- Corrigo Review, Verified User in Construction
9. eWorkOrders CMMS
eWorkOrders CMMS is a user-friendly solution that aims to simplify work order management, asset tracking, and preventive maintenance tasks. From what I’ve seen in G2 reviews, many users highlight the simplicity of the platform, making it an excellent choice for businesses that need an easy-to-use system without an overwhelming set of features. This simplicity seems particularly beneficial for teams where not everyone is tech-savvy, as the system integrates well into daily operations with little to no learning curve.
I frequently see G2 reviewers praise the query feature, which allows for efficient search and analysis of work order data. Many users find it helpful for filtering and retrieving specific information quickly, helping managers gain insights into work order trends, asset performance, and maintenance history. This functionality supports better decision-making and allows for optimized maintenance schedules, a feature that has received consistent positive feedback from users.
One standout capability that I’ve come across in G2 reviews is the trigger functionality. Users appreciate the level of customization it provides, enabling them to set up alerts whenever a customer creates a job via the customer login. Reviewers often mention the flexibility of this feature, as it allows teams to specify exact times, dates, and types of triggers, ensuring they only receive the most relevant notifications.
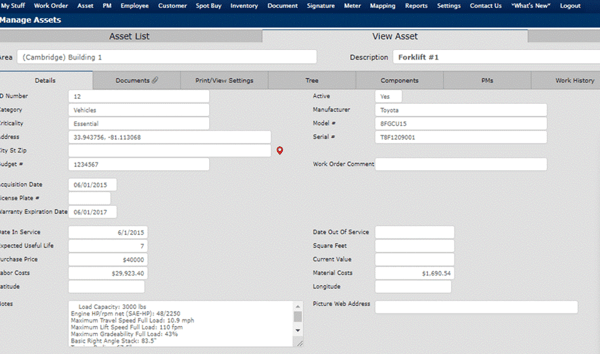
Despite the positive feedback, I’ve noticed users express dissatisfaction with the lack of custom report generation. Many G2 reviewers, including those who value data-driven decision-making, mention that the inability to create custom reports limits the platform’s flexibility. While the pre-designed reports are useful, they do not always meet the specific needs of all businesses, and the lack of customization in this area stands out as a drawback for some users.
In addition, a recurring theme in G2 reviews is the absence of auto-population for fields based on associated information. Users frequently note that automating this process could significantly reduce errors and save time, particularly when technicians are entering data. Many reviewers feel that this feature would streamline operations and improve data accuracy.
Another area where I’ve seen some users express frustration is the lack of automated vendor ticketing. G2 feedback highlights that currently, technicians have to manually send tickets to vendors when needed. Multiple users suggest that automating this process—where the system directly sends the tickets to vendors—would save time and prevent delays, making the process more efficient.
What I like about eWorkOrders CMMS:
- A consistent theme in G2 reviews is the simplicity and user-friendly design of eWorkOrders, which makes adoption easy, even for teams with limited technical expertise, ensuring smooth integration into daily operations.
- I’ve noticed that many G2 users appreciate the query feature, highlighting its efficiency in searching and analyzing work order data, which helps retrieve specific information and improve maintenance schedules.
What G2 users like about eWorkOrders CMMS:
"It’s a simple platform that suits our needs well. The other CMMS systems we reviewed had overly complex tools that would likely go unused based on our business needs and the skill level of our team. The option for an unlimited number of users is a game-changer, allowing even our entry-level technicians easy access to the platform without us needing to review the profit and loss every time we hire new staff. This was a major hassle with our previous platform, but EWO solved that issue."
- eWorkOrders CMMS Review, Logan C.
What I dislike about eWorkOrders CMMS:
- From what I’ve seen in G2 reviews, a common point of frustration is the lack of custom report generation in eWorkOrders. While pre-designed reports are available, users often feel the need for more tailored options to enhance the platform's flexibility.
- A frequent piece of feedback I’ve noticed is that eWorkOrders doesn’t auto-populate fields based on associated information, and many users suggest that automating this process would save time and reduce data entry errors.
What G2 users dislike about eWorkOrders CMMS:
"One primary concern is the learning curve associated with using the software. For individuals who aren't tech-savvy or used to working with digital tools, it may take some time and effort to become comfortable with the software's features and functionalities. This can lead to initial resistance and potentially slow down the adoption process."
- eWorkOrders CMMS Review, Verified User in Non-Profit Organization Management
10. Click Maint CMMS
Click Maint CMMS stands out for its simplicity in tracking work orders, repairs, and scheduled maintenance. From what I’ve seen in G2 reviews, users frequently praise the system for its ability to automate notifications for upcoming tasks, which ensures that maintenance activities are never overlooked. Many G2 reviewers seem to appreciate this proactive feature for keeping maintenance on track.
Based on feedback I gathered from G2 users, the reporting module is often highlighted as a key strength. Users find it incredibly helpful for managing maintenance costs and streamlining budget tracking. Multiple reviewers mention that the software’s asset tracking capabilities, including usage and condition monitoring, are valuable for planning future maintenance or replacements. Generating detailed reports within the platform seems to provide better insight into maintenance activities, which is appreciated by many users.
A common theme in G2 reviews is the ease of integration when transitioning to Click Maint from older systems. Many users note that the switch was smooth, with minimal disruption to daily operations. The onboarding process, which is well-supported, appears to facilitate a quick transition, allowing businesses to implement the system without significant IT resources or downtime.
I frequently see G2 reviewers highlight the mobile app's intuitiveness. Users especially appreciate being able to manage work orders and maintenance tasks from anywhere. This feature seems particularly valuable for teams with field technicians, providing flexibility for on-the-go management.
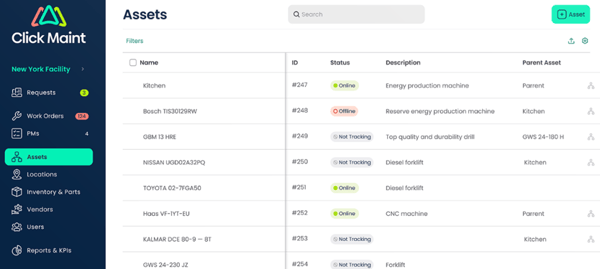
While the mobile app is well-received, I've noticed that advanced features could enhance the mobile experience. Many users on G2 point out that the app’s functionality could be more robust compared to the desktop version, which may leave some mobile-centric users wanting more.
Based on G2 reviews, I’ve seen some users express frustration with the absence of AI and predictive maintenance features. A consistent theme in these reviews is that incorporating AI-driven insights could help businesses anticipate maintenance needs and predict equipment failures more accurately. This capability would allow teams to perform preventive maintenance more efficiently, reducing downtime and minimizing costs.
Lastly, while the inventory management system is functional, I’ve come across noticeable dissatisfaction around its limited features. Users mention that a more comprehensive inventory system, with features like automatic restocking alerts and integration with procurement tools, would improve operational efficiency. Enhancing this functionality could help businesses prevent over-ordering or stock shortages, as noted in several reviews.
What I like about Click Maint CMMS:
- One standout capability, according to users, is Click Maint’s ability to track work orders, repairs, and scheduled maintenance, with automated notifications for upcoming tasks helping to stay proactive and organized.
- I’ve seen G2 reviewers highlight the reporting module as a key feature, particularly for managing maintenance costs and budgeting, making it easier to track asset usage and generate detailed reports for analyzing activities and costs.
What G2 users like about Click Maint CMMS:
"The best thing about Click Maint is how easy it is to manage work orders. Our implementation was straightforward, with only 6 users, and we were set up and managing work orders in about two weeks. The preventive maintenance feature is also simple to use and set up. The users love the mobile app as well."
- Click Maint CMMS Review, John R.
What I dislike about Click Maint CMMS:
- From what I’ve seen in G2 reviews, many users feel that the mobile app could benefit from more advanced features, with some suggesting that adding functionalities available in the desktop version would improve the experience for field technicians.
- I’ve noticed that inventory management is another area that could be improved. Users often mention the need for features like automatic restocking alerts and better integration with procurement tools to enhance operational efficiency and streamline inventory tracking.
What G2 users dislike about Click Maint CMMS:
"I would like to see more features in the mobile app, as not all the features available on the desktop version are currently accessible on mobile."
- Click Maint CMMS Review, Matt T.
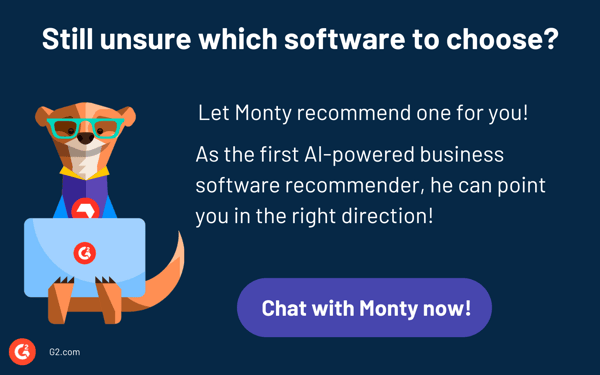
CMMS software: Frequently asked questions (FAQs)
1. What are the two types of CMMS?
The two main types of CMMS are on-premise CMMS and cloud-based CMMS. On-premise CMMS is installed on local servers and provides full control but requires maintenance. Cloud-based CMMS is hosted online, offering remote access, automatic updates, and scalability with lower upfront costs.
2. How does CMMS software work?
CMMS (Computerized Maintenance Management System) software helps organizations manage maintenance tasks, track assets, schedule preventive maintenance, and generate reports. It centralizes work orders, logs equipment history, and streamlines inventory management to reduce downtime and improve efficiency.
3. Is Excel a CMMS?
No, Excel is not a CMMS, but it can be used for basic maintenance tracking. However, it lacks automation, real-time alerts, and advanced reporting features found in dedicated CMMS software, making it less efficient for managing large-scale maintenance operations.
4. Which is the best free CMMS software?
UpKeep is one of the best free CMMS software options, offering essential maintenance management features for small teams. To explore more free CMMS tools, check reviews on platforms like G2.
5. Which is the best mobile CMMS software?
Some of the best mobile CMMS software include MaintainX, Limble, UpKeep, and Fiix CMMS. These tools offer mobile-friendly interfaces, real-time work order tracking, and remote access, making maintenance management easy on the go.
6. How long does it take to implement CMMS maintenance software?
Implementation time varies based on company size, data migration needs, and user training. Small businesses may take a few weeks to fully integrate CMMS software into their operations, while larger organizations can take several months.
Equipment breaks, but your sanity doesn’t have to!
After thoroughly evaluating the best CMMS solutions, I’ve come to appreciate just how much the right system can transform maintenance operations. Each platform offers unique features tailored to different needs—whether you’re focused on asset tracking, predictive maintenance, or improving team collaboration. With so many options available, there’s always a solution that can streamline your maintenance processes.
But here’s the reality—no matter how efficient your CMMS is, maintenance will always be an ongoing task. Equipment will break down, work orders will pile up, and unexpected issues will arise. Without a CMMS, managing all of this can be overwhelming. Yet, with the right system, you can stay ahead, reducing downtime and keeping operations running smoothly.
I hope my insights help you find the right CMMS for your organization—because, let’s face it, no one likes dealing with constant maintenance headaches!
Integrating robust help desk software with your CMMS can help you address issues faster and keep operations running smoothly.